铅酸蓄电池从最初发明到现在已历经一个半世纪了。某些基本的工艺,尤其是活性物质的生产,的确显得过于古老。不过,古老绝不意味着简单。
过去30年中凡是参与到铅酸蓄电池设计和制造的人都知道,随着市场要求的不断变化,当前各种铅酸蓄电池的制造和处理方法已是千变万化,新设计层出不穷,尤其是在用于诸如电信和叉车行业等细化的目标市场时。我们有许多铅酸蓍电池技术方面的大师,正是通过他们的辛勤研究工作才引导我们更好地理解铅酸电池的神秘。我们现在能够更好地理解铅粉制造、合膏和固化过程以及合金成分对各种铅板栅生产方法的效应、安全运行及对阀控电池的理解等过程中的复杂机制,不但如此,我们还可以对它们进行控制。
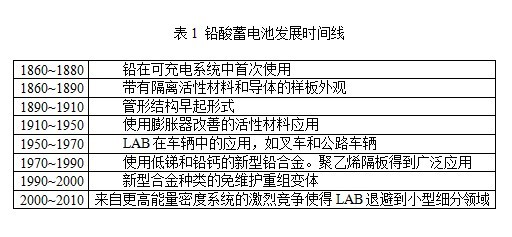
我们有理由相信是市场的力量主导了铅酸蓄电池的设计、材料和技术方向。通过对所使用的基于铅的材料以及工艺参数对其化学、结构和同素异形类型的影响的系统调查,我们可以生产出能够更好适应特定市场需要的蓄电池。
例如现在我们已经知道,三盐基或四盐基碱式硫酸铅的浓度以及α和β氧化铅的同素异形类型能够在活性材料制造期间予以控制。这些工艺可以进行优化,以用于汽车固定或牵引用途。但是,当销售蓄电池的利润与销售一块塑料盒装的铅取得的利润相同时,几十年来的艰辛工作和针对这一知识的创造性研究就可能会被完全抛弃。
铅酸蓄电池的演化和发展促进了不同材料之间的复杂结合。这主要包括铅及其衍生物,活性材料的有机和无机添加剂,用作箱、盖、隔板的塑料,以及现在用来改善蓄电池性能的其他成分。为了安全、经济地处理这些材料,获得最佳效率和最低的环境影响,就需要了解有关材料特性以及所要求的处理方法的详细知识。
就处理方法和所用材料而言,还需要考虑其它因素。这包括生态和经济因素,以及性能要求。铅有毒,要受国际植物保护公约的监管,是一种受控物质。这要纳入到设备设计和操作人员的作业方法之中,按照流程说明和严格的培训方法执行。
就经济因素而言,之所以选用铅酸蓄电池,原因之一就是其价格。工艺必须采用流线型,产生最低的废料,并有保修要求,在大多数工厂中对底线的影响要超出对生产率的影响。
工艺优化目的旨在详细考察用于特定蓄电池应用的材料、工艺和设计。本文还将阐述如何以成本效率、安全高效的方式优化这些工艺、说明、作业方法和设备,以适合特定要求。
铅酸蓄电池对制造工艺造成挑战主要是因为生产过程中所用的原材料变化。氧化铅含有25%~35%的自由铅,诸如塑料盒等塑料具有+/-1.5mm的容差。同一个制造商生产的隔板可能会含有12%~18%的油。
对铅酸蓄电池之间的性能均匀性的要求也越来越高了,这主要是因为串联和并联连接的需要,尤其是在电信和备用电源市场中。除此之外就是现代牵引充电器中使用的过充电系数降低了,使得串联连接的电池均匀性几乎成为不可能。
为了使生产的铅酸蓄电池满足使用时的具体要求,需要考虑和优化许多方面的问题。设计、材料、处理方法、控制和质量体系、安健环等方面等都得考虑到,以确保符合性能和法律要求。下面将轮流介绍每个工艺过程:
铅氧化物生产
有两种生产氧化物的基本方法:巴顿锅和球磨机。使用巴顿锅时,将会得到成比例的α和β氧化铅,其比例大小取决于操作条件以及铅丹和铅。在球磨机技术下,得到的几乎全是β氧化铅,其中铅的含量为25%~35%。
我们可以对参数进行控制,且巴顿锅和球磨机两种方法下氧化物的自由铅含量变化能分别控制在5%和10%以内。与巴顿锅相比,球磨机法氧化物具有不同的粒径分布和形状因数,通常情况下球磨机法氧化物的酸吸收能力更强。
合金铸造
现在有众多的铅板栅合金在使用,根据蓄电池设计的不同,包括从含有辅助元素(如锡、砷、银、碲等)的铅钙合金,到含有更常见的锑加晶粒细化剂合金元素的牵引合金。这些合金具有不同的板栅生产要求,尤其是模具设计、铸造和预制方法,甚至是撇渣程序。不正确的撇渣程序,尤其是对铅钙合金来说,会撇掉昂贵且有益的合金元素,如锡、铝、钙、银等。漂浮在铅上的大多数物质,确切说是金属和金属间化合物,都具有较低的密度,它们将会沉淀出并漂到铅锅表面。
在某些情况下,去掉这些元素将会使板栅的机械性能变差,抗腐蚀能力减弱;并且,如果达不到合金的成分要求,随后的时效、涂膏、固化和成型过程将会起到有害的作用,至少是一种金钱上的浪费。在某些情况下,蓄电池生产商向供应商支付一定的合金费后,将差不多30%的合金金属扔回到金属渣中。这更多的是在租用元素而非购买元素,除非租用对蓄电池制造商来说并无益处。另一方面,他们也会拥有非常忠诚的铅供应商。
合膏
这个阶段会非常容易出错。混合程序和温度对膏剂构成的化学形态和晶体结构有着直接的影响。虽然现在还无法确定具体的反应过程,但经简化的反应过程将会如下:
在较低温度条件下,通常是低于70℃,稳定的碱式硫酸盐是三盐基硫酸铅;在较高的温度条件下,形成四碱式硫酸铅,其原因可能是与氧化铅反应并失水。
晶体式硫酸盐和组成取决于氧化铅和酸的比例以及混合温度。SLI膏剂混合倾向于具有比牵引膏剂更低的比率和膏剂密度。膏剂的混合参数将可决定蓄电池的冷启动能力和循环寿命,应仔细予以控制。
合膏添加剂
膏剂添加剂主要包括黑烟末、硫酸钡、木素磺酸盐和胶粘纤维。木质衍生物有很多变种,如橡木粉,以及最新的人造木素磺酸盐替代品。膨胀剂的基本作用就是防止有孔物质在循环期间闭合,改善充电电压端和絮状物,为膏剂材料提供黏合剂。
其数量和比率会根据具体应用(循环或冷启动应用)的不同而不同。膨胀器的生产方法也同样重要,因为它会影响蓄电池的寿命,尤其是在牵引应用中。
涂板
当将膏剂涂到板栅上时,必须得到正确的机械特性,以便让膏剂具有足够的切变强度,容许仅使用涂膏送料斗的挡板移动就可将膏剂从送料斗压入移动的板栅中。大部分的切变强度均来自于碱式硫酸盐的晶体结构,混合作业期间可以增加碱式硫酸盐。可由膏剂混合操作工实施的简单试验就是抓一把新鲜膏剂并用手挤压。如果感觉到膏剂具有易碎质地,则可知道需要增加足够的机械一体性。
这一阶段的膏剂具有较高的含水量,在急骤干燥过程中会去掉其中的一部分,8%~11%的含水量是正常的,这也在一定程度上取决于膏剂中使用的氧化物类型。
固化
急骤干燥器通常会通过将含水量减少到其中的水分正好能够催化氧化剩余的自由铅的水平来启动放热固化反应。
氧化铅在水中可溶,板孔中剩余的水分会在其蒸发过程中渐渐地在多孔基体中重新分配氧化铅,从而形成胶合剂,将碱式硫酸盐结晶固定到一起,有助于增强结晶体与板栅之间的黏合力。
现代的做法是使用固化炉,对于牵引和汽车板来说循环时间均少于24小时。成型循环参数最终通常是自由铅含量小于2%.含水量小于1%。
管式极板填充
牵引管式正极采用红色和灰色氧化铅干粉混合物填充,有时会添加少量铅黄或湿/浆填充系统。就这些系统的相对价值,现在仍有广泛的争论,不过干式填充更为普遍,因为它操作相对简单且成本低廉。采用湿式填充方法时,经常要考虑健康和安全问题。这里的关键参数是管子的填充密度以及材料在板中的分布。在确定最终含水量和活性材料密度时,湿式填充方法对管子强度和多孔性非常敏感。不正确的填充会对蓄电池的循环寿命产生严重后果,尽管也能得到适合板容量的合适活性材料重量。
采用干式方法填充的板,可以用稀酸对其进行酸洗,令其更加便于处理并帮助降低初始形成温度。务必小心避免板栅接触面处出现敦化作用。
蓄电池组装
下一步主要就是一些机械性处理工作,涉及隔板材料的塑性焊接和连接以及箱盖焊接等。正负极板通过在夹具中焊接汇流排或使用铸焊汇流排法连接。这一阶段容易出现许多错误,尤其是在用铸焊汇流排或手工焊接来连接板时,铅钙容易出现问题且要求非常清洁的接线片,最好是在添加汇流排铅之前熔化并浸沾焊料。
正确理解塑性焊接和软化原理对于确保良好的箱盖焊接来说至关重要,工具整定以及来料的尺寸检查也是关键因素。经验表明,一般的压力试验方法并不是检查泄漏或薄弱/劣质焊接的安全方法。必须采用其他的方法来实施检查。
成型和酸洗
很可能出现的情况是已经正确地完成了这步之前的每个过程,却在此因错误的加酸和充电做法而毁掉了先前的所有努力。不管是单次成型还是一次成型法,都必须确保板栅/镅接触面处不会出现钝化层,同时,板中不会留有多余的硫酸盐。正极板上在固化或酸洗过程中遗留的任何自由铅也必须在这一阶段清除掉,以防加速自放电。
其中关键因素包括:启动充电过程之前的浸泡次数,使用内化成时的冲酸密度,板间电流密度,加工温度,以及间歇和放电步骤。
生态
因为铅有毒,使得设计过程和设备变的有些困难。相关制造商们正受到越来越大的压力,要求确保逐步降低空气中的铅值并减小铅排放量。设备设计、工作方法和工人教育是首要考虑的因素。
如果可能,有必要按照标准的人类环境改造学惯例对工艺进行设计,以消除工人和铅之间的任何接触,并最大程度地减小在制造过程中的任何阶段与氧化铅的接触。最近在中国境内关闭的众多蓄电池工厂警示我们必须重视这些规定。
欧洲理事会规范中有关来自烟囱的铅酸排放的规定现在也越来越严格了,企业也正在承受更大的压力,不得不增加取样率并负责监视和降低对周围环境的影响。强制要求企业实施自我评价,否则不予发放lPPC许可,尽管自我评价法现在越来越贵并愈加复杂。
流程和质量说明
有必要采用清楚准确的说明来指导实施良好的工作惯例和程序。不过,写的再好的说明也不能保证万无一失。制造过程高度依赖操作人员的培训和自觉。
任何质量检查程序和方法都不能防止所有的质量问题和质量退返。我们无法检查蓄电池里面的质量,看起来是“好蓄电池”没什么意义,对于启动器来说这是个错误的动词。制造一只好的蓄电池意味着做这项工作的人知道他在做什么,并想接照正确的方式来做这项工作。
这或许是最难实现的事,但的确有必要。不是由说明或机器来制造蓄电池——而是由人来制造,没有受到良好激励和培训的生产团队,很难完成制造工作。
铅酸蓄电池仍在继续发展,不管这是一种自然选择还是一种遗传工程亦或是两者兼之:制造方法和工艺也必须改进,以满足处理新材料的需要并符合要求更高和更具挑战性应用的性能要求。
(责任编辑:朱竹)