随着我国经济社会的发展及人民生活水平的提高,我国的铝易拉罐消费量逐年增加,2007年已超过二百亿只,并以指数式地递增。相应的废铝易拉罐的回收量也越来越大,据不完全统计,近年已达到十几万吨。众所周知,铝易拉罐的罐体是3004牌号的铝合金、罐盖是5182牌号的铝合金,这些铝合金都是用优质的原生铝配制而成的。而目前我国回收的铝易拉罐都被降级使用,制成了副牌的A102、ADC-12、非标铝锭等档次不高的铝合金锭,使其真正的价值没有达到有效利用,在经济上造成很大的浪费。如果能把回收的废铝易拉罐通过保级还原熔炼制备技术制成符合国家标准的3004牌号铝合金,再用这些铝合金通过热轧、冷轧、成型等工艺技术重新制成新的易拉罐,实现重复循环利用,这样不仅做到了废铝易拉罐的高值化的利用,而且还有良好的经济效益和社会环境效益。
由于3004牌号铝合金的性能指标要求高、生产难度大,例如,按标准,其抗拉强度要达到 260 MPa,延伸率要达到3%以上,在生产中制罐成型时破罐率不能超过百万分之五(即5个PPM级),所以到目前为止,国内还没有用废易拉罐铝生产3004牌号铝合金的再生铝企业,也没有一条用废铝易拉罐生产高值化铝合金的自动化或半自动化的生产线。
随着再生铝产业的飞速发展,科技创新成为推动产业升级的强大动力,越来越多的再生铝企业投入到了研发专利、技术创新、掌握自主知识产权的生产实践中来,如蓄热式燃烧、低温熔炼等许多节能减排新技术新工艺在再生铝行业内得到了推广和普及。在集成创新理念的指导下,许多跨国界、跨行业、跨领域的新理念、新技术、新工艺正在被产学研一体化的研发企业集成整合,未来几年再生铝行业酝酿着重大的技术突破。
废铝易拉罐保级还原熔炼制备技术在国外已有较成熟的技术路线,像美国波尔公司等大型企业早在上世纪九十年代就已建成了一整套先进的生产工艺流程和技术装备,但其造价过于昂贵,国内还没有一家再生铝企业引进利用。为了早日建成符合我国国情的废易拉罐铝循环利用生产线,依据我所整合自主创新的多项国家发明专利技术和实用新型专利技术,借鉴和吸收国外先进的技术理念,研究设计了一整套具有中国特色的废易拉罐铝保级还原熔炼制备技术与生产工艺流程,在这里抛砖引玉,与大家共同探讨。
一、废易拉罐铝循环利用生产线技术路线
根据废易拉罐铝的成分与外形特点,技术路线主要由三大部分构成:预处理技术、熔炼配制技术和铝熔体精炼净化及晶粒细化技术。每个部分又由多个技术环节组成:
1. 废易拉罐铝预处理技术
废易拉罐铝及废易拉罐铝打包块的破碎(粉碎机)——易拉罐铝的分选(荧光分选机)——易拉罐表面除漆(脱漆窑)——废气二次燃烧和净化(热量回收、干法收尘)——回转筛分振动脱碳(强力振动筛)
2. 废易拉罐铝熔炼配制技术
计算机配料(电脑软件配料)——侧井投料(蓄热式双室双循环熔铝炉、机械循环泵)——低温熔炼法熔铝
3. 铝熔体精炼净化及晶粒细化技术
炉内精炼变质(铝合金复合精炼变质法)——炉外在线除气(在线除气设备)——过滤(陶瓷过滤板)——细化晶粒——浇铸成板锭或板坯(半连铸法)
二、废易拉罐铝循环利用生产线的工艺流程
用保级还原熔炼制备技术处理废易拉罐铝的生产线主要工艺流程如下:
1. 预处理技术路线
由于回收来的废铝易拉罐成分和外形都相当复杂,特别在我国的废品回收体制下,混杂了许多的非铝杂料,因此必须对这些回收的废易拉罐原料进行必要的预处理。在废铝易拉罐的预处理技术上,一些发达国家已形成了一套较完整的生产工艺,如美国的波尔公司,采用了多项先进技术,使废铝易拉罐在无污染的情况下得到了快速有效的处理,我们借鉴了此类成功的技术路线,取其关键技术的要点,并利用国产设备完成这条接近国际先进技术标准的预处理生产线。
废易拉罐铝的破碎工序。由于质地较轻,为了便于运输和存储,绝大部分回收到的废铝易拉罐的外形都已破坏或被压成饼料,在回收企业中常用的和进口的废铝易拉罐大多也已经打成压块。由于饼料及压块整体除漆时会造成除漆不充分,而且会导致废铝易拉罐料的局部过烧,影响其冶金质量,所以在除漆之前必须对废铝易拉罐进行破碎处理,使其漆面外露,便于除漆。
本生产线拟采用江苏某厂出产的PS-1型箱式粉碎机进行机械粉碎,该设备每小时可处理1~2吨铝料,可直接破碎易拉罐压块,解决了传统设备只能破碎单个易拉罐的难题,提高了生产效率。工作时将饼料或压块,经传送带由上方的加料口直接填入粉碎机,经处理后得到2~3厘米左右的碎片,并经输送带运至下道分选设备。
废易拉罐铝的分选工序。在废铝易拉罐的回收中常常会不可避免带有少量的铁罐等非铝料,也就是在废铝易拉罐中,有部分罐体的材料是软铁料,压块后更难以区分,因此粉碎后的铝碎片中不可避免会带入含铁件等非铝料。由于3004合金对杂质铁的有严格的要求,所以必须在投炉前把带铁的原料分选出来。
本流程拟采用上海某企业的最新产品MST X55B型荧光分选机,来实现废易拉罐的分选。这种技术的分离精度可达5×10-5(即分选误差仅为十万分之五),目前这样的精度达到了国际领先水平。铝碎片经传送带成批进入荧光分选设备,利用激光(X射线荧光)的高分辨能力,高速识别,并通过压缩空气气吹分离的方法清除废铝易拉罐中夹带的非铝杂物和含铁件。经分选后的净化铝碎片经输送带运至下道除漆设备。
废易拉罐铝的表面除漆工序。废铝易拉罐表面的漆层,含有不少有害重金属元素和碳氢化合物。他们不仅会给铝液带进有害杂质和气体,影响合金质量;而且燃烧产生的有害烟气也给熔炼时的环境带来严重污染。破碎后的碎铝片漆面暴露在外,很容易与空气接触反应,而且它具有很低的热容量,使其能在很短的时间内就升到除漆温度,致使漆分解、碳化,而不影响到基体铝片的冶金质量。本流程拟采用河南某厂生产的旋转式脱漆窑,分选后的碎铝片由输送带迅速送入并通过精确控温(正负不超过5℃)的脱漆窑中,一般脱漆窑的温度控制在300℃~500℃左右,罐料在炉内迅速升温,在短时间内达到除漆温度,致使罐料表面的漆分解、碳化。开始时需要加一定的热能,当达到一定温度之后,热能就主要依靠易拉罐表面漆炭化过程的放热来维持。在旋转式的脱漆窑中,易拉罐的漆层被炭化,依靠旋转过程的自身振动,碳化后的漆层脱落。并且在此过程中废易拉罐中的残留的水分也得到烘干,消除了后工序的熔炼过程中的水和铝水起反应的可能,使冶炼质量和生产的安全得到保证。
废气二次燃烧工序。脱漆窑所产生的烟气温度一般在300℃~500℃左右,因此烟气中除粉尘外还含有大量漆层热反应后所产生的有害气体和可燃气体,会给环境带来严重污染,直接排放显然不行。因此,在烟气排放前,将烟气接入二次燃烧设备,进行处理。我所和江苏某环保设备厂联合研制的TQ-2型二次燃烧处理设备,使烟气直接进入一个高温加热室,瞬间被加热到1150℃左右,使烟气无害化焚烧,也将其中未燃尽的漆粉末进行充分燃烧,并将燃烧后的烟气导入换热器(管形蜂窝状),将热量转吹入回转窑中,使最后排除的烟气低于180℃,基本不含二噁烷(致癌物质)等有害气体,并热量得到充分利用。在烟气处理的末端,采用旋风喷淋塔对所进入的烟尘处理,第一步用旋风式收尘器,使大部分粉尘得到回收,第二步用喷淋过滤技术,在喷淋过滤塔中,烟尘得到彻底的回收,使最后排放的烟气达到国家二级排放标准。
除漆后废易拉罐铝的脱碳工序。由于各种原因,经烘干碳化后的易拉罐碎片上还会残留部分漆碳化后的碳粒,需再处理以获得高度洁净的铝片料。我们的研究表明,采用了我们确定的表面除漆工序后,碳化的漆层与铝基体的结合力已明显降低,采用强力振动可实现铝基体和碳化漆层的分离。本流程拟采用河南某厂出产的2YK1000型强力振动筛,每小时可处理碎铝片2吨左右,经除漆后的铝碎片进入强力振动筛强搅拌,通过强力振动使炭粒全部脱落分离,获得了高度洁净的铝片料。
2. 废易拉罐铝熔炼配制技术路线
熔炼技术路线的基本任务,就是把预处理后的铝碎片投入熔铝炉中,经过加热和熔化成为熔体,再对熔化后的熔体进行成分调整等处理,最后得到成分合乎标准要求的铝合金液。而这项任务的关键在于,采用行之有效的工艺与设备把铝碎片在熔炼时的烧损、能耗和环境污染尽可能的降到最低。
计算机配料工序。铝制易拉罐是由罐体和罐盖咬合加工而成的,高122mm,直径66mm,壁厚0.13mm,重14.93克(体11.21克,盖3.38克,拉环0.34克)。易拉罐的成分主要由三种铝合金组成:易拉罐的罐体与罐底是3004铝合金,罐盖是5182铝合金,拉环是5042铝合金,其成分及含量见表1。
表1 易拉罐各组成部分及废铝易拉罐混熔的化学成分
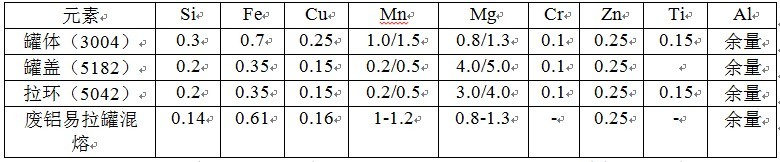
注:Mn、Mg为主要强化元素;Si、Fe、Cu、Cr、Zn、Ti均系为杂质元素
常规回收的废铝易拉罐很少带有拉环,成分可忽略不计,但罐体和罐盖的材料不同,在生产使用中也很难将罐体和罐盖分离,所以,配料思路上,基本按3004合金、5182合金外加部分双零铝来进行配制。由于每批次原料的成分略有差异,配料前也可取少量已洁净化的碎料(不少于1吨)重熔,以得到近似的各元素平均值用作配料参考系数。
在实际生产中建议使用计算机软件配料。这种方案利用计算机的灵活性和精确性,依据多年实践经验,从再生铝熔炼特点出发编制而成,加上原料数据库(1 500~2 000炉次的技术数据),有效地解决了配料难题。
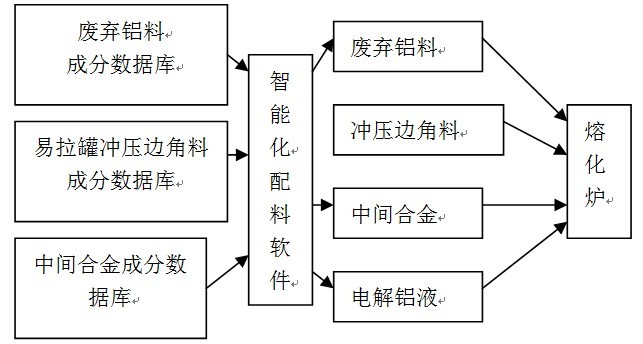
图1 计算机智能配料流程图

同时,为提高一次达标的配料成功率还应注意原料数据库的建立:就是对不同批次、不同来源的已洁净化的易拉罐废铝料的成分、质量状况进行检测、统计,并输入计算机,形成原料数据库。表2是15吨重熔再生3004合金配料单的实例,表3是配制熔炼后获得的重熔再生3004合金锭成分与美标要求的成分对照。
从上表3可以看出,易拉罐废铝重熔再生3004合金在化学成分上是可以达标的。但需注意的是,双零铝加入的多少,关键在于Mg元素值的高低,其他元素成分均有较大的调整空间。
废易拉罐铝的投炉工序。
目前废铝易拉罐料在我国的常规使用中,大部分企业都是采用直接投炉,有的是将压块压入铝水中,有的是将饼料装袋直接撒入,但由于密度低,都无法避免铝料漂浮在铝液上,因此铝耗往往居高不下,并由于严重氧化,也影响着铝液的冶金质量。
为了解决这个问题,熔铝炉拟采用我所自行研制并已获得国家专利的蓄热式双循环双室熔铝炉,该炉是针对以轻薄铝为主料而设计的节能型低损耗熔铝炉。
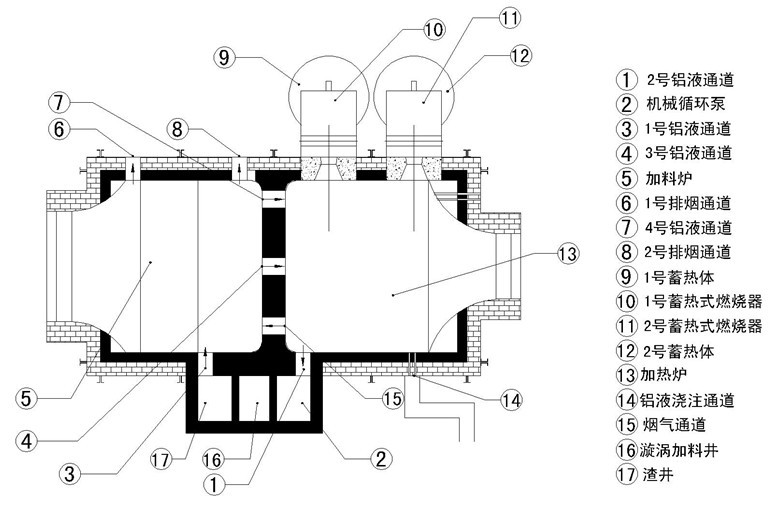
图1 蓄热式双循环双室熔铝炉结构图
双室指的是一个加料室和一个加热室;所谓双循环,一是指炉气循环、二是指铝液循环,这两种循环方式是分别通过蓄热式燃烧设备和机械循环泵来实现的。引入蓄热式燃烧技术,因其自动调节炉压的特点,使火焰不直接加热所投物料,而是通过两室间的烟气通道,使炉气的循环转动间接预热物料;引入机械循环泵,将加热室的热铝水通过外池打入加料室,用热铝水冲刷刚投入的铝料,使其熔化陷入铝水中,并且还在外池中设置了漩涡沉熔井,铝液从加热室内由机械泵打入侧井,在漩涡井金属流产生向下的漩涡,迫使加入的易拉罐碎片迅速沉入金属液面下,与外界的空气隔离,大幅度提高了溶入率,实现了低损耗的易拉罐碎片的熔炼。通过这样的二个投料方式,碎铝料通过机械泵漩涡沉熔加入,大的打包料通过炉门加入无火焰的加料室,使铝耗降低到最低程度,能耗也大大减少,真正达到了节能减排,低耗高效的目的。
实践表明,通过蓄热体这一媒介,出炉烟气的余热被转换成空气的物理热而得到回收利用,烟气排出温度可降到150℃,空气可预热到800℃左右的高温,热回收效率达到85%以上。这样不仅可以节约大量能源,还可以大大提高燃料的理论燃烧温度,缩短熔炼时间,减少烧损率。加上其他相应的节能措施的综合效果,燃料可节省30%以上。并且,由于炉气含氧量得到了有效的控制,铝液的烧损也相应得到控制,在理想状态下,铝耗可降低2~3个百分点。 再加上,双室双循环炉加上铝液循环泵和漩涡加料井,有效地解决了低密度碎薄料的加入方案,大幅度提高了易拉罐碎片的溶入率,使得总铝收得率最佳可达97%以上。
低温熔炼技术在废铝易拉罐熔炼的应用。国内一些再生铝企业在熔炼易拉罐废铝时,为了使加入的高熔点合金元素(如3004合金中的锰)能充分溶解入铝液,往往将铝液温度提高到850℃~1050℃,把炉膛烧的通红,然后再投料,工人这样做的目的是为了加快熔化速度。这样会产生两个问题:一是高温加速了铝及各种合金元素的氧化烧损,加大了铝及合金元素的损耗,还因高温下铝液表面的氧化膜失去了保护功能,铝液吸气严重,导致铝液冶金质量恶化;二是为了提高铝液温度,能耗也势必大幅度增加。同时,为保证铝液的冶金质量,又必须加大精炼变质的力度,增加精炼剂和变质剂的用量,延长处理时间,这样又进一步提高了铝液的处理成本。因此,生产过程中使用我所自主研发的国家发明专利“再生铝低温熔炼法”,简单说就是采用适当的温度下用适当的搅拌方法,来加快合金元素的溶解,实现再生铝在630℃~730℃下熔炼和调质,从而实现了高效率低能耗,并获得优质的铝液。
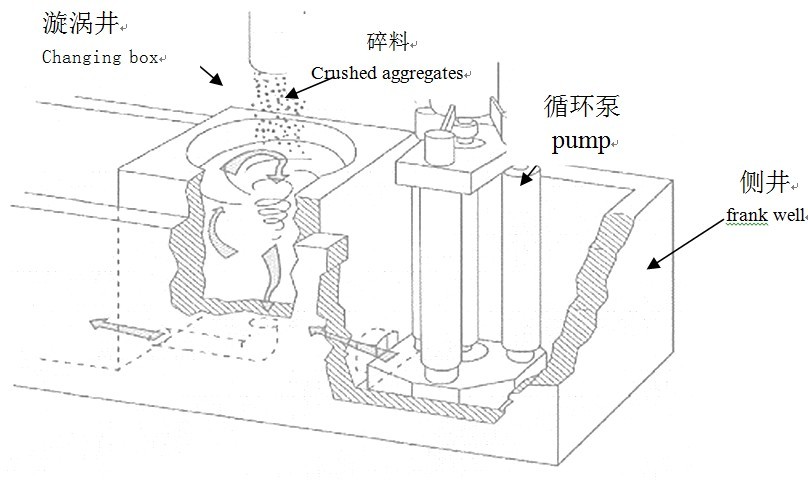
图2 机械循环泵和漩涡加料井技术方案示意
3. 铝熔体精炼净化及晶粒细化技术路线
精炼净化就是采取相应的精炼变质措施控制铝液的冶金质量,使其针孔度、氧化夹杂及金相组织符合规定要求的优质铝合金液;细化晶粒则是使获得的3004合金具有更好的综合机械性能,既要有高的抗拉强度,还要有很好的塑性和延展性。
炉内精炼变质工序。在熔炼过程中精炼变质方法采用由我所的国家发明专利技术“铝合金复合精炼变质方法”为主体的“稀土复合精炼变质处理生产技术”来进一步提高再生铝冶金质量。它根据不同稀土元素的不同特性,巧妙地搭配形成复合精变剂。既发挥某些稀土元素变质功能,实现长效变质和细化晶粒,改善了性能;又利用某些稀土元素高电负性及储氢特性,在铝熔体中固氢及去除氧化夹杂,实现对熔体的净化并能维持5~7小时,使精炼变质效果达到了最佳状态,有效地改善了铝合金的冶金质量和性能。这种复合精变处理工艺不产生有害废气及有毒物质,并减少铝在处理中的烧损,大大减轻了环境负荷,降低了生产成本,从而成为了真正绿色集约化的铝合金熔体复合精变处理工艺。并且,由于稀土独特的属性,不仅改善了铝熔液体的冶金质量,提高了性能,还能使废品率大幅度下降,这些都为废弃的易拉罐再生熔炼,重新制成能满足冲压易拉罐要求的3004铝板坯提供了重要的质量保证措施。
炉外在线除气工序。铝合金熔液在精炼后仍存在少量氢气、固体废金属杂质物等有害物质,特别在半连铸生产线上,铝液必须通过一定长度的流槽进行浇注。在这个浇注流动过程中的吸气和氧化,会使铝液出现二次污染,使铸件形成气孔、疏松、夹杂等缺陷,直接影响铝件的物理性能、力学性能以及使用性能,因此有必要对浇注过程中的铝熔体进行在线净化处理,除掉这些有害物质。
本流程的炉外在线除气系统拟采用湖南某厂出产的HKLDU-Ⅱ型在线除气净化装置,将该装置接于铝液流槽,当铝水通过净化箱时,石墨转头会伸入铝液对其进行除气处理,效果很好。
铝熔体过滤工序。在炉外在线除气装置的后端会使用浙江某厂出产的铝液专用陶瓷过滤板,过滤粒径达50µm左右,可进一步过滤铝液中的固体杂质,净化浇注前的铝液。
铝熔体细化晶粒工序。细化金属凝固组织不仅可以提高材料的力学性能,而且可以改善成分及组织的不均匀性、减小缩孔和疏松、减小热裂倾向,改善材料的后续加工性能。促进金属生核是低耗高效地改善金属凝固组织的关键。目前常规的细化晶粒都是采用AlTiB中间合金来增加合金液中的结晶核心,从而达到细化晶粒的目的。我们的研究表明,脉冲电流和脉冲磁致振荡可使合金结晶凝固时大量增核,可十分显著地细化各种金属材料的铸态组织。并由于它是一种物理场增核,因此对环境和铸锭(坯)均无污染,现场应用方便,成本低,有效改善成分偏析、杂质富集,减小热裂倾向,减小缩孔和疏松,是金属凝固组织细化的理想的工艺。该技术已取得专利,并在生产实践中得到了应用,获得了科技进步奖。生产过程中拟选用这种行之有效的物理场技术和常规的AlTiB细化技术相结合的路线,使再生的3004合金板坯的性能更上一个台阶。
三、结论
本条废易拉罐铝保级还原的熔炼制备生产线,能生产满足轧制易拉罐罐体的达到ASTM美国标准要求的3004合金铸坯。
这条废易拉罐铝保级还原的熔炼制备生产线的技术方案切实可行,工艺流程简捷可靠,技术装备造价不高,大约几百万人民币,可以为国内的再生铝企业所接受。
本技术路线集成了先进的蓄热式熔炼技术、低温熔炼及稀土复合精炼变质等专利技术,并配备了具有自主知识产权的废气二次燃烧及多级烟气处理技术的环保设备,组成了一条清洁化的生产线,大幅度降低了能耗、铝耗,避免了有害气体对环境的严重污染,大大提高了废铝易拉罐的使用价值,是一条可达到高值化利用的绿色环保生产线。
(责任编辑:朱竹)